Does your factory or plant experience a lot of downtime? Do you keep seeing repeated bearing costs appearing in your invoices? If it’s happening regularly, it can get expensive, trigger unplanned downtime and result in lost production, increased maintenance costs and additional spare part inventory.
Constantly replacing bearings that are actually designed to last a long time is frustrating and with the associated costs, it can soon mount up. Think about the wheel bearings on your car, how often do you have to change them? Most likely never. Wheel bearings will typically last 100,000 miles or more if properly looked after and serviced regularly.
If this was your car, you wouldn’t accept it if the wheel bearings were constantly failing.
So how long should bearings last?
There is actually a formula for how long bearings should last but if bearings are properly looked after and maintained to the highest standard then you could expect bearings to last up to 12 years or possibly even longer in some cases.
So why are your bearings not lasting this long you may ask. How is this even possible?
We’ll get to that but first, have you also noticed that you are paying for a lot of lip seals? It’s likely you haven’t noticed as they are quite inexpensive, but it might be worth checking up on. So what do lip seals do? Lip seals basically seal the space between the stationary and rotating parts of rotary equipment such as a pump, mixer or similar. The idea is that they contain the lubricant and help to protect it from contamination. This is exactly how it works, certainly to start with anyway.
Look at your sealing methods on your equipment. If the maintenance team are using lip seals then it is quite possible that it is a major contributing factor of the failures.
A lip seal will over time wear on the shaft or shaft sleeve forming a groove and therefore loses the ability to ‘seal’, which not only creates expense on reworking or replacement costs in itself but also leaves the bearings exposed to contamination.
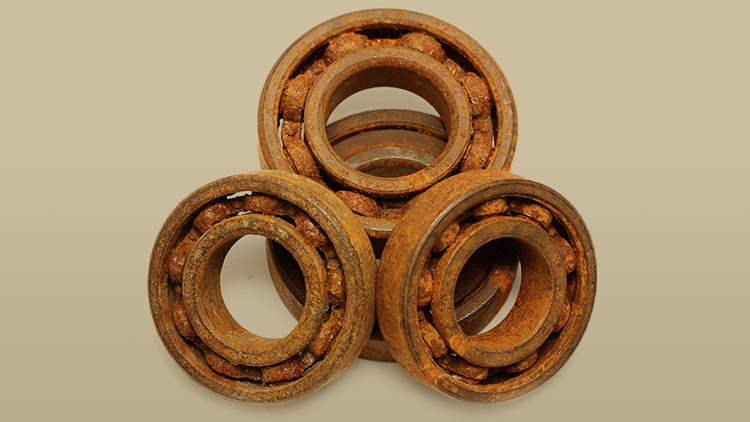
So what is this contamination and why is it happening?
Well, it is most likely to be water, process fluid or just general dust and dirt; it could be from cleaning or the process itself but this is what is typically getting into your bearing and causing them to corrode and in turn break down in quick succession. This is what happens when the lip seals start to wear creating gaps that then allow leakage.
So what can you do to stop it?
There are a couple of ways of increasing the mean time between failures (MTBF) on the bearings. The first is to increase the maintenance time spent on looking after the bearings; this could be changing the lip seals more frequently as part of a good maintenance routine. Maintaining a good seal at all times will help to ensure that the bearings are suitably protected. This method however will see an increase in maintenance costs and increase wear to the shaft or sleeve the lip seal rubs against, which will in turn create a need for additional repair or replacement costs.
Alternatively there are products called bearing protectors or isolators that are non contact and will still completely seal and protect the bearing from any contamination. Once fitted, they give the ultimate protection and will last for as long as the bearings without the need for constant maintenance. They are a bit more expensive than a lip seal but the cost saving benefits of bearing protectors far outweigh the initial cost.
By opting for bearing protection and installing them correctly on your equipment, you will see this item once on an invoice - typically lasting many years until you see the next one. Reducing your purchasing, administration time and labour costs.
Read more on..... how much lips seals are costing you